PROCESSING FOR THE CONSTRUCTION OF
STAINLESS STEEL TOTE TANKS
Among the strengths of Ginalco Srl, a leader in the field of stainless steel tote tank construction, is its strong specialization in aluminum and stainless steel processes.
The approach is never standardized. The company’s stainless steel tote tank production model is strongly tailor-made, ensuring that each tank produced is the result of close design collaboration with the customer. This ensures that each tank is fully customized, responding precisely to the customer’s specific requirements.
Ginalco’s construction of stainless tanks is distinguished by meticulous attention to detail and years of experience in working with aluminum alloys and stainless steel.
Stainless steel tote tank production: highest quality standards
To ensure high quality standards in our tanks, we adopt state-of-the-art manufacturing processes, which include innovative techniques and first-rate materials. This commitment to excellence ensures that Ginalco tanks not only meet but exceed our customers’ expectations for durability, efficiency, and custom design. One of the key processes that allows us to achieve excellence in the construction of our stainless tanks is precision welding, employing advanced technologies to ensure flawless joints and lasting strength.
Stainless tank welding is done under strict quality control, using only the highest quality materials that ensure structural integrity and compliance with the most stringent safety standards.
It is precisely because of the expertise we have acquired over the years that our welding for stainless tanks stands out from the alternatives on the market. Attention to detail and the ability to meet specific design requirements are what enable us to create customized solutions that enhance functionality and aesthetics
The adoption of advanced technologies and close cooperation with customers are fundamental pillars in our philosophy. Our experience and dedication in the industry enable us to meet and overcome the most complex challenges, providing tailor-made solutions that perfectly match the operational needs and standards required by the market.
To ensure high quality standards, we use the following production stainless steel tanks:
Manual
and semi-automatic TIG (Tungsten Inert Gas) welding process.
- Arc welding with infusible electrodeprotected by inert gas, which allows the fusion of two edges of base material with or without filler material.
Process used in both direct current (stainless steel) and alternating current (aluminum alloy). Ginalco also performs the TIG welding process of aluminum alloy in direct current for special processing.
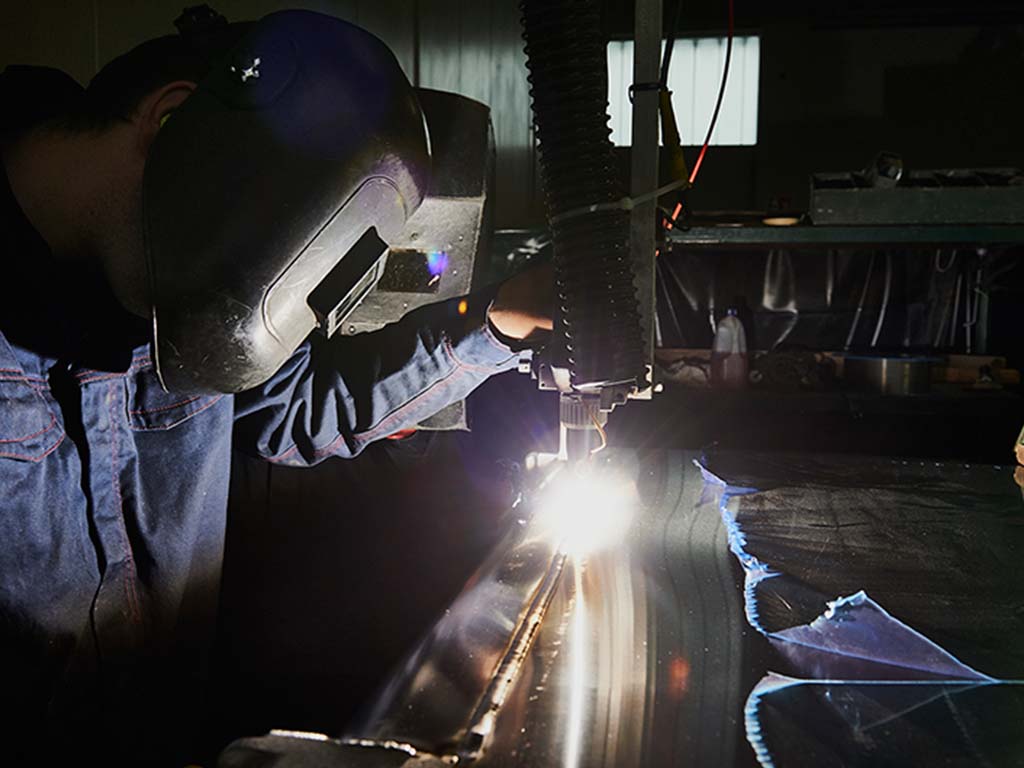
Manual welding procedure MIG/MAG
(Metal-arc Inert Gas/Metal-arc Active Gas)
- Arc welding with metal, protected by inert gas (MIG) or active gas (MAG) for increased joint penetration.
Pure (inert) argon is mainly used for aluminum alloying.
Argon/helium mixture used for welding stainless steel.
It enables high productivity, resulting in reduced costs.
Our state-of-the-art welders enable high weld bead quality, with virtually zero spatter presence.
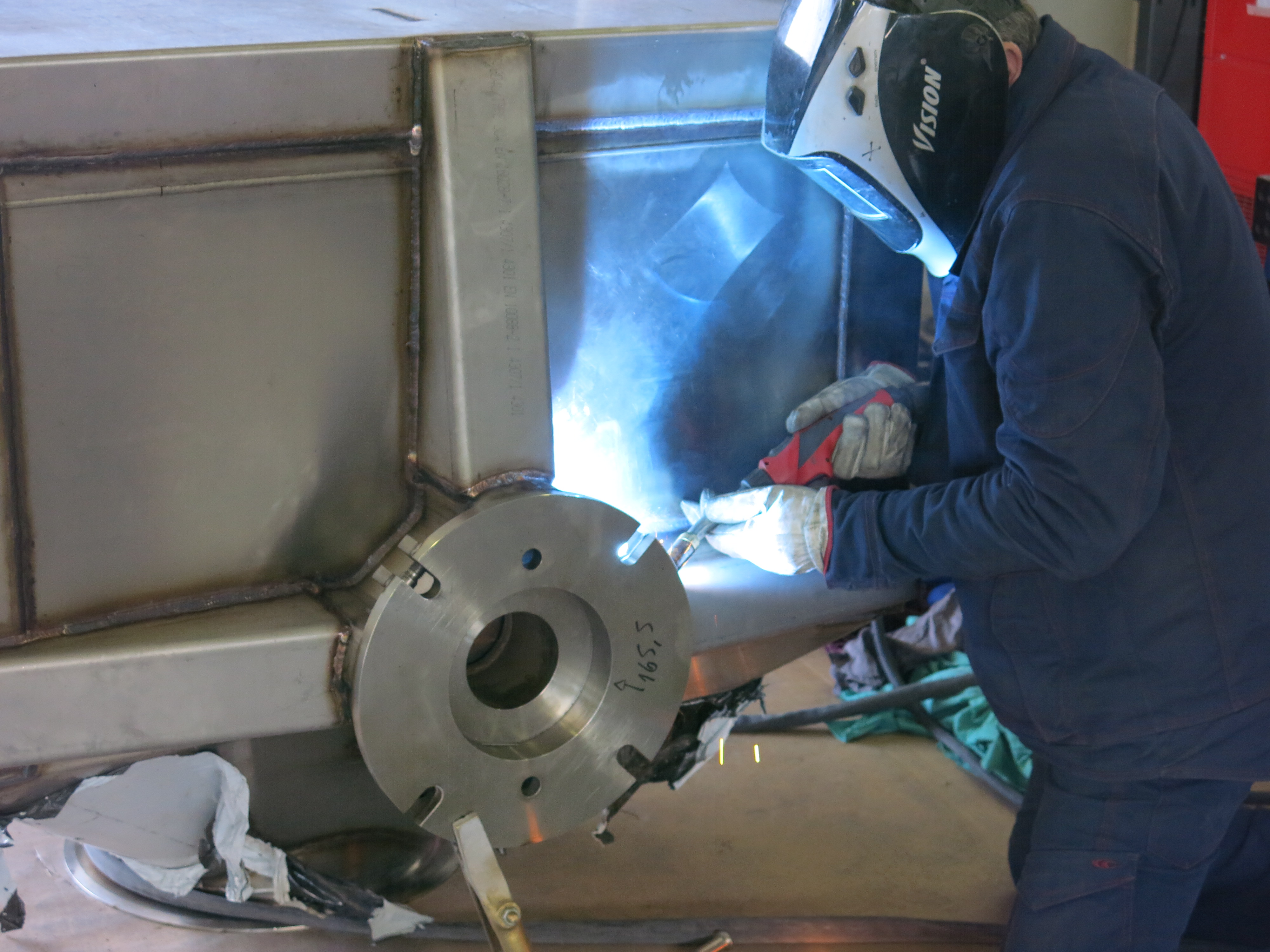
Sheet metal finishing process
- Stainless steel tanks, can have the weld seam completely removed flush with the sheet metal and achieve different quality levels of finish, up to mirror polish. Other possible finishes are pickling, passivation, and electropolishing of stainless steel.
Aluminum alloy containers generally need only brushing off the oxide caused by welding. However, we can also remove aluminum alloy weld seams if required by customer specifications.
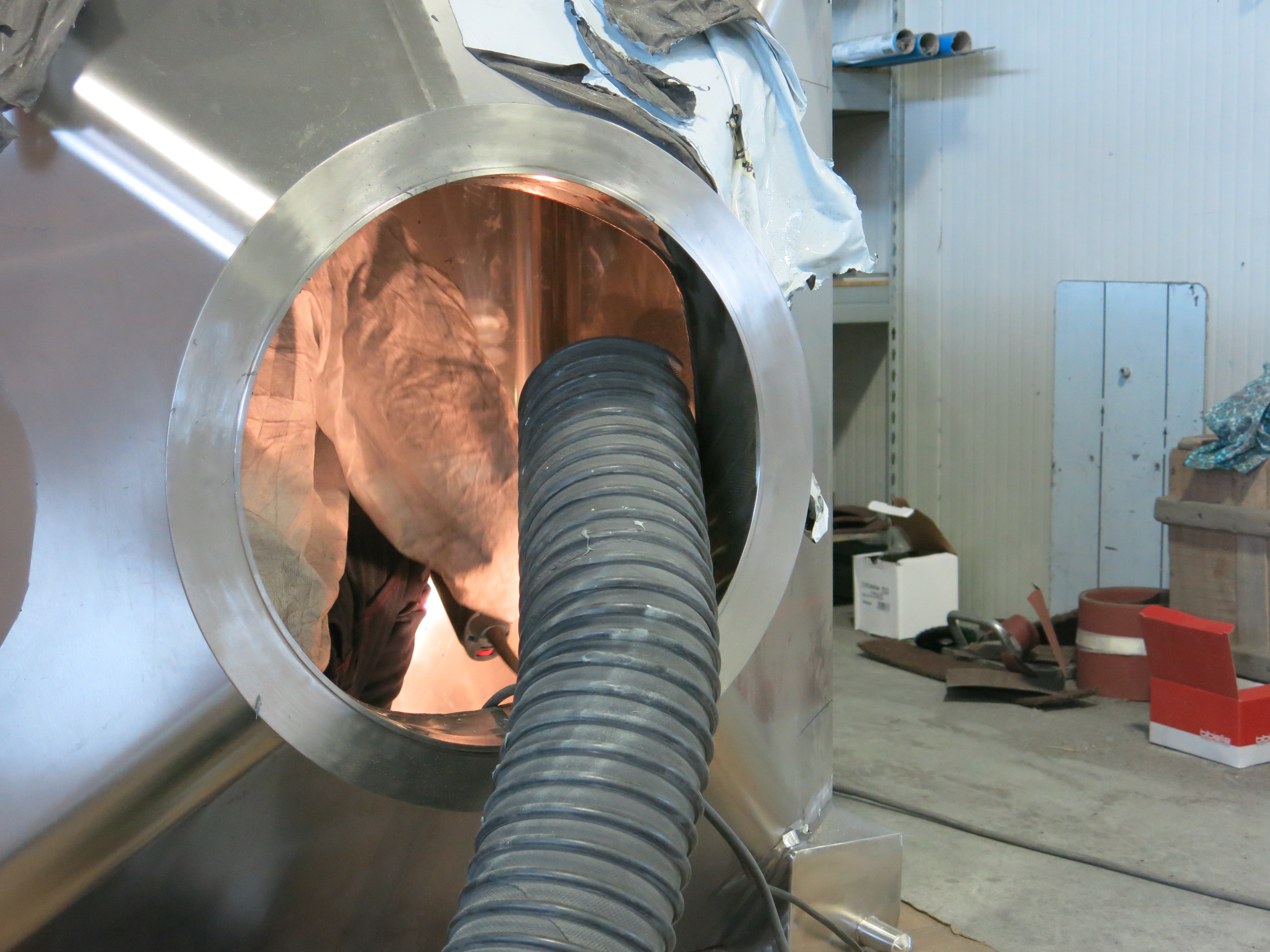